WASHINGTON — A hiring wave, process overhauls, and new tools and equipment have helped a U.S. Air Force base cut by more than half the time it takes to repair and overhaul F-35 engines, from an average 244 days to 106.
And the commander of the base’s Oklahoma City Air Logistics Complex hopes that in two years, if it gets the necessary resources, Tinker Air Force Base will be able to repair anywhere from 105 to 120 F135 power modules per year. That would be more than double the 51 it handled in 2021, Maj. Gen. Jeffrey King said in a May 26 interview. The air logistics complex is a massive facility at Tinker — the largest of three depots in Air Force Materiel Command — that maintains a variety of aircraft and engines for the Air Force, including the F135.
A scarcity of working and available F135 engines has plagued the F-35 Joint Strike Fighter program and increasingly dragged down the jet’s mission-capable rate.
The Government Accountability Office told Congress in April that, across the military’s fleet, F-35s were unable to fly due to a lack of spare parts for about 17% of the time in fiscal 2020 and fiscal 2021. A lack of functional power modules — the engine’s core, which contains key controls and components that generate the thrust to propel the aircraft — was the top reason those F-35s weren’t mission capable, the watchdog agency said.
Improving the capacity of depots that perform the heaviest maintenance on F135 engines is one of the key ways the military is trying to tackle that worsening shortage. By far, Tinker AFB’s Heavy Maintenance Center handles the most F135 maintenance work. The military is also trying to reduce the amount of necessary work on engines, in part by extending how long they can stay on a jet before they need to receive maintenance.
“The reduction of flow days from 244 down to … 106 [between the beginning of 2021 and today] was not by accident, and it was not by just lobbing off fat,” King told Defense News. “It was a deliberate, meticulous application of [process improvements]. We changed up how we inspected parts when they were removed, we changed how we trained our personnel. We redesigned shop floors and redesigned shop processes to eke every day out of the production process to go faster.”
The F-35 Joint Program Office in fall 2020 put in place a plan to fix the engine’s sustainment troubles, focusing on improving depot capacity and keeping engines on aircraft longer.
Tinker also increased the number of power modules it maintains each year, from 14 in 2020 to 51 in 2021. This year, King said, it’s likely to turn around more than 70, beating its goal of 60. And next year he hopes the depot will be able to finish about 90, paving the way for it to hit between 105 and 120 in 2024.
Jennifer Latka, vice president for the F135 program at Pratt & Whitney, which makes the engines, said in a May 18 interview that the military’s investment in depots got a slow start because the F-35′s engines performed well initially. But that meant when the engines started having problems, the depot capacity wasn’t there to handle them, she said.
Over the last two years, she explained, the military and the company focused on improving depots’ ability to maintain more engines. And this year, she added, all sites maintaining F135s — including Tinker, Naval Air Station Patuxent River in Maryland, Edwards Air Force Base in California and international sites — are expected to beat their combined target of 122 engines, far more than the 76 all sites maintained last year.
‘Tricks of the trade’
In early 2021, Tinker personnel, the F-35 Joint Program Office and Pratt & Whitney began mapping out processes used to maintain engines, said Bobby Hager, director of the 544th Propulsion Maintenance Squadron at Tinker. At the same time, they kept an eye out for bottlenecks that led to extra work, or otherwise hindered how fast the center could turn around engines.
Base personnel found several constraints, she said, including sluggish training for mechanics. They also realized several types of equipment necessary to disassemble and reassemble engines weren’t available on the shop floor, Hager added.
“We realized that, as we get deeper and deeper into the maintenance of this engine, there were certain critical pieces of tooling that we either didn’t have available or didn’t have experience with, just because we’ve never used it before,” said Lam Dinh, the F135 propulsion flight commander in the 544th. “Some of those [assembly] toolings were new to us, as we were learning how this engine goes together or comes apart.”
The lack of equipment and of proper specialized training was felt most acutely during heavier work, King said.
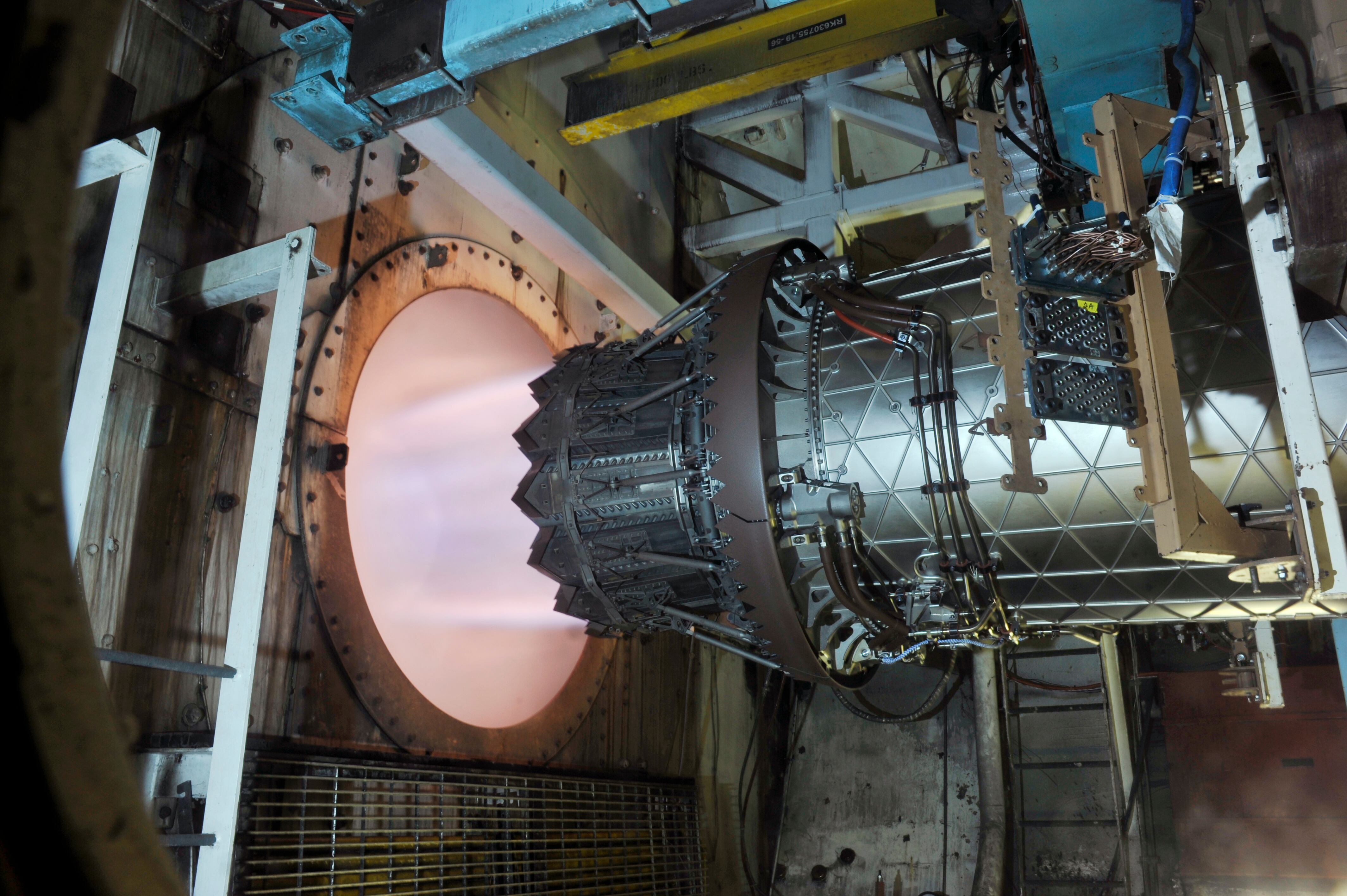
The center is working to get more of the right kind of equipment into mechanics’ hands, Hager said. But in the meantime, officials are reorganizing processes so work is performed at different times, when some of that equipment is available.
King said Tinker mechanics have traveled to Pratt & Whitney sites, including in Middletown, Connecticut, where the engines are built, to “learn tricks of the trade.” Those visits helped Tinker personnel pick up subtle techniques that quicken and improve the assembly process, he added, and they are now cataloguing those lessons to share with a new F135 maintenance center set to open at Naval Air Station Jacksonville in Florida.
Latka said the Jacksonville site will handle a comparable number of engines to Tinker when it comes online in a few years.
As Tinker personnel work on engines, they are also replacing older turbine blades with fresh blades featuring a new coating that better resists degradation from salt and sand. This became an issue in the Middle East and during deployments at sea.
Latka said about 35% of the F-35 fleet now has blades with the new coating, up from roughly 25% last October. The entire fleet should have the fresh coating by 2030, she added, if not sooner.
Faster responses, more hires
Two years ago, when Tinker needed Pratt & Whitney to clear up an engineering or process question, King said it could take up to two weeks to get an answer. Now, he said, the company tends to answer complex questions in two days, if not in minutes — if the right engineer is on the shop floor.
And that was another issue altogether.
Tinker faced a challenge when it first started working on F135 engines in 2015, Dinh explained: It had experienced mechanics working on aircraft engines, but none on that specific mission, and virtually no outside experts it could hire.
And so the base turned its attention to training its mechanics on the engine in as short a time as possible by “micro-gating” — an approach that breaks down a process into several smaller tasks in order to better train mechanics on each individual step. This meant mechanics would repeatedly perform the steps until they could excel at them, Dinh said.
Dinh said this was better than trying to teach mechanics “to soak everything in all at once, and at the end of the day, get nothing out of it.”
King agreed it was advantageous. “That depth brought about proficiency, which brought about speed and quality.”
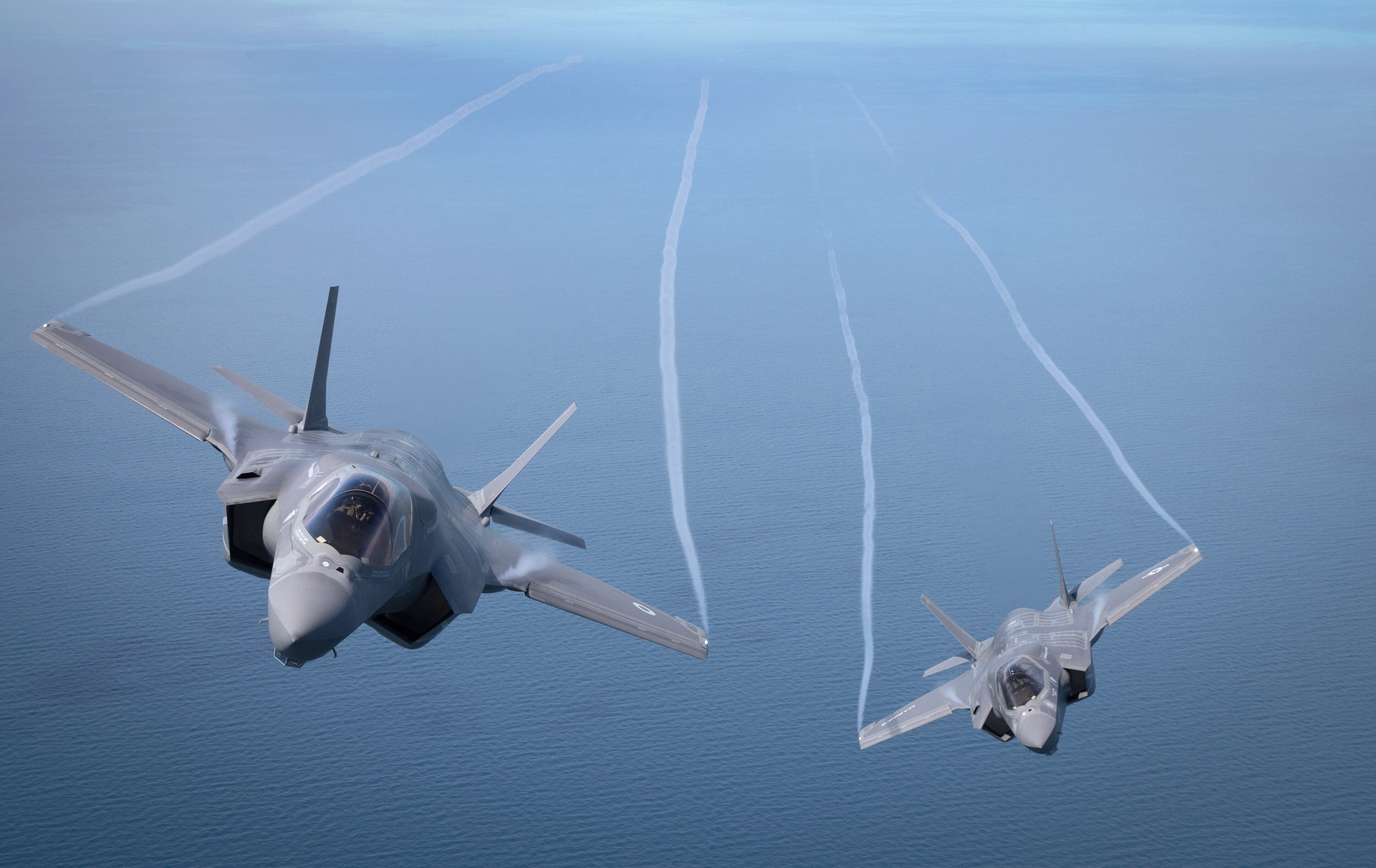
Tinker has also dramatically increased the number of mechanics working on F135s — and has plans to bring in more.
Dinh said that when he started working on the program around the beginning of 2017, there were about 17 other mechanics working on F135s there. As of about a year and a half ago, that workforce had grown to 79 over a single shift.
With 103 mechanics now focused on the F135, Tinker added a limited second shift and expanded the number of power modules it could work on simultaneously from nine to 21. All but three of those mechanics are civilians, which provides more continuity since they don’t get transferred every few years, King said.
Tinker plans to hire several dozen more mechanics over the next few years so the base can work on 30 power modules at once, King added. Funding, equipment and tools are also on the way to allow the base to handle those additional engines, he said — essentially doubling the size of the current shop.
King said plans are under consideration to expand Tinker’s capability to maintain 40 engines at once, though that effort hasn’t received funding.
And in 2024, Tinker expects to begin conducting preventative engine maintenance scheduled in advance at full scale, with about a handful of scheduled engine removals planned for 2023. Currently, only unscheduled engine removals — that is, repairs that must be done when problems arise — are performed on F135s, King noted.
But above all, King explained, Tinker will keep looking for ways to bring down the cost of maintaining F-35 engines. Pratt and Whitney said it’s found ways to cut the cost of the F135′s first scheduled maintenance visit by about 40%, which it said would save more than $14 billion over the life of the program. Those cost-saving strategies include extending the life of parts until their next maintenance cycles and finding new ways to repair engine components that avoid replacing parts with new spares.
“Now that we’ve gone from a pediatric to an adolescent engine, cost control is exceptionally important, especially as we field more F-35s and put more F135 engines into the field,” King said. “We’ve got to go faster, the quality needs to stay high. But we’ve got to do it cheaper.”
Stephen Losey is the air warfare reporter for Defense News. He previously covered leadership and personnel issues at Air Force Times, and the Pentagon, special operations and air warfare at Military.com. He has traveled to the Middle East to cover U.S. Air Force operations.